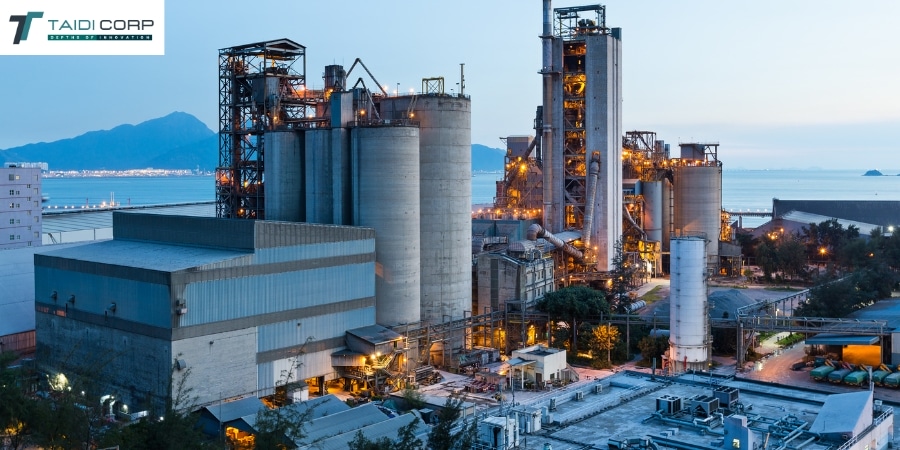
Industrial sectors often require reliable and efficient water extraction methods, especially in areas where surface water resources are limited. Deep well submersible pumps are a robust solution for such applications. This guide provides a critical perspective on using deep well submersible pumps effectively in industrial environments, covering their selection, installation, and maintenance.
Understanding Deep Well Submersible Pumps
What is a Deep Well Submersible Pump?
A deep well submersible pump is a type of pump that operates underwater, typically used for extracting water from deep aquifers. It is designed to be placed inside a well casing, fully submerged, allowing it to push water upwards efficiently. This pump type is crucial for industrial operations requiring a steady and high-capacity water supply.
Industrial Applications of Deep Well Submersible Pumps
Deep well submersible pumps are extensively used in various industrial sectors, such as:
- Mining: Ensuring water supply for mineral processing and dust suppression. For more information on their role in the mining industry, you can visit The Role of Deep Well Submersible Pumps in the Mining Industry.
- Agriculture: Providing irrigation solutions for large farmlands.
- Manufacturing: Supporting processes that require a continuous water supply, such as cooling systems and chemical processing.
Choosing the Right Deep Well Submersible Pump
Key Factors to Consider
- Well Depth and Pipe Size: The depth of the well and the diameter of the well casing are critical factors in selecting a suitable pump. A mismatch can lead to reduced efficiency and potential damage to the pump. Ensure that the submersible pump’s specifications align with the well’s depth and pipe size.
- Flow Rate and Pressure Requirements: Calculate the water demand of your industrial operations to determine the required flow rate and pressure. Underestimating these parameters can lead to insufficient water supply, while overestimation may result in increased operational costs.
- Motor and Impeller Type: Choose a motor and impeller that match your industrial needs. Submersible pump motors are designed for durability and efficiency under high-stress conditions. The impeller type affects the pump’s performance in terms of flow rate and energy consumption. For more insights into choosing the right impeller, you can refer to Submersible Pump Impeller Types.
Installation Best Practices
Step-by-Step Installation Guide
Proper installation is crucial for the optimal performance of a deep well submersible pump. Here’s a brief overview of the process:
- Pre-Installation Inspection: Check the well for any obstructions or damages. Ensure that the well casing is intact and free from debris.
- Pump Preparation: Assemble the pump and motor, ensuring all components are securely attached. Double-check the connections of the submersible pump cable to prevent any electrical issues.
- Lowering the Pump: Gradually lower the pump into the well using a sturdy winch system. Keep the pump straight to avoid tangling the submersible pump pipe and cable.
- Securing the System: Once the pump is in place, secure it with a well cap and ensure all connections are watertight.
For a more detailed guide on this process, visit How to Install Deep Well Submersible Pumps: A Detailed Step-by-Step Guide.
Maintenance and Troubleshooting
Regular Maintenance Tips
To maximize the performance and lifespan of deep well submersible pumps, regular maintenance is essential. Key activities include:
- Routine Inspections: Check for any signs of wear and tear, such as unusual noises or vibrations, which could indicate issues with the submersible pump motor or impeller.
- Cleaning and Lubrication: Periodically clean the pump and lubricate moving parts as per the manufacturer’s recommendations.
- Electrical Checks: Inspect the submersible pump cable and connections to prevent electrical faults.
For more expert advice on maintenance, refer to Expert Maintenance Tips for Maximizing the Performance of Deep Well Submersible Pumps.
Common Problems and Solutions
- Low Water Pressure: This could be due to a clogged impeller or worn-out submersible pump motor. Regular cleaning and timely replacement of worn parts are crucial.
- Pump Overheating: Often caused by insufficient cooling due to low water levels in the well. Ensure the submersible pump is fully submerged and check the well water level regularly.
- Electrical Issues: Faulty wiring or a damaged submersible pump cable can lead to frequent shutdowns. Regularly inspect and replace damaged cables to maintain a reliable water system.
For long-term reliability tips, check out Long-Term Reliability Tips for Deep Well Submersible Pumps: Ensuring Consistent Performance.
Ensuring a Reliable Water Supply
To maintain a consistent and reliable water supply in industrial applications, it is essential to:
- Monitor Water Levels: Regularly check the well water level to ensure the submersible pump is operating within its designed parameters.
- Implement a Backup System: Consider having a secondary pump or water source in case of pump failure, minimizing downtime and maintaining operational efficiency.
For more strategies on ensuring a reliable water supply, you can read How to Ensure a Reliable Water Supply with Deep Well Submersible Pumps.
Conclusion
Deep well submersible pumps are invaluable assets in various industrial applications, providing reliable and efficient water extraction. By selecting the right pump, following proper installation procedures, and adhering to regular maintenance practices, you can ensure optimal performance and longevity of your water system. For comprehensive deep well services and support, consult experienced professionals to tailor solutions that meet your specific industrial needs.