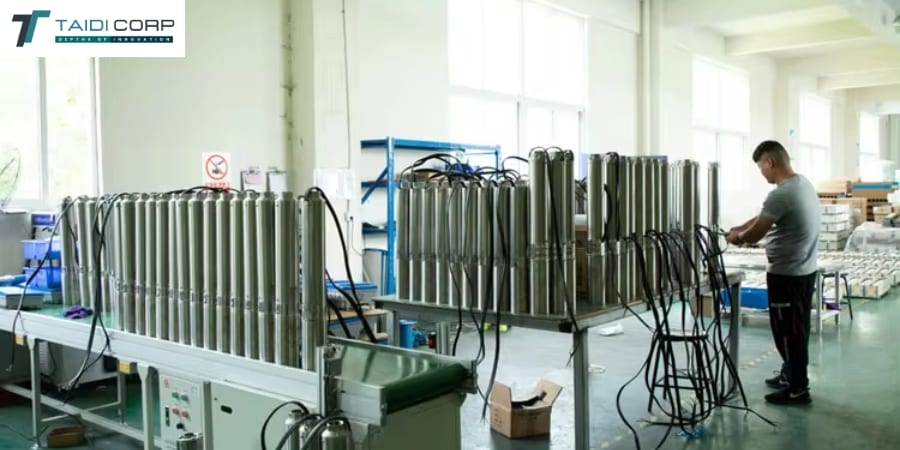
Motor failures in deep well submersible pumps can pose significant challenges, especially for farmers, homeowners, and industries that rely heavily on consistent water flow from deep well systems. These issues are not just inconvenient—they can be costly if not properly addressed. Understanding common motor problems and their solutions is crucial to maintaining the long-term performance of your deep well submersible pump.
Common Problems in Deep Well Submersible Pump Motors
1. Overheating of the Submersible Pump Motor
A frequent cause of motor failure in deep well submersible pumps is overheating. Submersible pump motors are designed to work underwater, where the water helps to cool the motor. When water levels drop or the pump runs dry, the motor can quickly overheat and fail.
Solution: Installing a thermal protection device is one way to prevent overheating. These devices automatically shut off the motor when it reaches unsafe temperatures. Monitoring water levels regularly and installing sensors that can alert you when water levels are too low can also prevent this issue. For detailed guidance on maximizing pump performance and avoiding overheating, read our Expert Maintenance Tips for Maximizing the Performance of Deep Well Submersible Pumps.
2. Power Supply Issues
Fluctuations in power supply can lead to motor failure in deep well pumps. Irregular voltage or frequent power outages can cause the motor to burn out or malfunction.
Solution: Installing a voltage stabilizer is critical for maintaining a consistent power supply to your deep well submersible pump. You should also ensure that your pump’s electrical connections are secure and regularly inspected. A control box equipped with surge protection can also safeguard against voltage spikes. Learn more about troubleshooting pump problems in our Comprehensive Troubleshooting Guide for Deep Well Submersible Pumps.
3. Corrosion and Wear of Motor Components
Over time, exposure to hard water or corrosive materials can cause significant damage to the motor components, leading to failure. This is especially problematic in submersible pump systems exposed to hard or mineral-heavy water sources.
Solution: Regular inspection and cleaning of the motor components are vital for preventing corrosion. Installing a filtration system can reduce the amount of debris entering the well, prolonging the life of the motor. For a detailed approach to dealing with hard water in deep well systems, check out our guide on How Deep Well Submersible Pumps Handle Hard Water.
4. Bearing Failure
Bearing failure is another common issue that affects submersible pump motors. This can be caused by improper installation, inadequate lubrication, or exposure to contaminants in the well.
Solution: Ensure that the pump is installed correctly by following a precise step-by-step process. Regular maintenance, including lubrication and cleaning, can prevent bearing wear. If you suspect improper installation, refer to our Detailed Step-by-Step Guide to Deep Well Submersible Pump Installation.
Preventative Measures for Long-Term Motor Performance
1. Regular Inspection and Maintenance
Routine maintenance is key to avoiding motor failure in deep well submersible pumps. Regularly inspecting your system, cleaning components, and ensuring that all parts are in working order will help extend the motor’s life. Scheduled maintenance should include checking the submersible pump impeller, control box, and other critical components.
Solution: For a comprehensive maintenance schedule, consider reading our guide on Effective Deep Well Pump Maintenance, which outlines the necessary steps for keeping your pump in optimal condition.
2. Using Quality Parts and Components
Cheap, low-quality parts can accelerate wear and tear on your motor. Using high-quality pump components, especially in harsh environments, is essential to minimizing breakdowns.
Solution: Make sure you are familiar with the key components of a submersible pump. Our Detailed Guide to Pump Components provides a breakdown of all essential parts, including the motor and impeller.
3. Testing the Pump Performance Regularly
Regular performance testing helps to identify early signs of motor failure. Monitoring flow rates, pressure levels, and electrical performance can help you catch problems before they escalate into more serious issues.
Solution: Make sure to perform regular tests on your deep well submersible pump to assess its performance. For a deeper understanding of performance testing, visit our guide on Testing the Performance of Deep Well Submersible Pumps.
Conclusion: Proactive Steps to Prevent Motor Failures
Motor failures in deep well submersible pumps can be disruptive and costly, but they are often preventable with the right approach. By understanding the common causes of motor failure—such as overheating, power supply issues, corrosion, and bearing failure—you can take proactive steps to protect your investment. Regular inspection, using quality parts, and maintaining a consistent power supply are all critical factors in ensuring long-term performance.
To learn more about maintaining and troubleshooting your deep well submersible pump, explore our extensive resources, including Comprehensive Troubleshooting Guide for Deep Well Submersible Pumps and Regular Cleaning and Inspection for Deep Well Submersible Pumps.
By following these steps, you can ensure the continuous operation of your deep well water system, whether for residential, agricultural, or industrial use.